Shift Toward Standardized System Solutions for Military Ground Vehicles
Military ground vehicle interconnect solutions are shifting from custom, one-off designs to systems comprised of readily available standardized components. Standardized options can handle applications faster, better and more economically.
Current Market & Practices
A shifting battlefield is challenging the traditional approach to platform design in military ground vehicles, which play an integral role in modern militaries. Today, vehicle interconnect solutions are highly sophisticated and designed to withstand the harshest environments ground forces will encounter, including extreme temperatures, water immersion, vibration, shock, fire and more. Wiring harnesses and complete interconnect solutions form the backbone connecting critical command and control functions. Presently, however, multiple sub-systems (like radar, communications and GPS) in the same vehicle all operate independently of each other and are often incompatible.
A lack of standardization across vehicle fleets can result in inconsistent Human Machine Interface (HMI) — including crew controls, displays and connectivity — while also leading to increased training and maintenance costs, in addition to more time spent on both. Each driver or operator is trained specifically for their vehicle, with service, maintenance and spare parts also unique to that vehicle. In critical situations this prevents platform sharing of common parts between vehicles, thereby reducing the number of available vehicles to a ground fleet as damage is incurred and systems are affected.
Interconnect systems are made up of numerous unique parts which presents inventory and stocking challenges, further delaying a damaged vehicle from returning to service. These systems are in service for many years and are subject to significant upgrades as requirements frequently change to address new threats, scenarios and technology. Additionally, as current and future ground vehicles demand more sophisticated onboard communication systems, power distribution, and active protection systems, more electronics lead to space constraints within the vehicles. All of these issues lead to a significantly higher cost of ownership throughout the vehicle’s lifecycle. full bitstream signature-based authentication.
Shifting Landscape
Drive Toward Standardization
To reduce defense spending and homogenize platforms, many governments are driving toward standardization. These new standards are already beginning to redefine electrical interfaces used in advanced military ground vehicles. Several countries leading the charge with examples of vehicle and system architecture specifications mandated on all new programs include:
• United Kingdom: UK MOD Defense Standard 23-09, Generic Vehicle Architecture (GVA)
The initiative specifies the mandatory standards for the design and implementation of land vehicle platform electronic and power infrastructures, physical interfaces, HMI and Health & Usage Monitoring Systems (HUMS). The use of GVA was first applied in Ocelot (Foxhound) armored vehicles enabling quick and easy electronics and wiring replacement.
• United States: US VICTORY
This standard defines a set of open standards developed by a government-industry partnership for interfaces and component types. VICTORY represents a combination of C4ISR (command, control, communications, computers, intelligence, surveillance, reconnaissance) and EW (electronic warfare) with a DataBus-centric approach.
• Australia: DEF (AUST) 11297
Australia’s approach maximizes the use of open, modular and scalable hardware and software by using a generic combat system architecture and wiring replacement. This is very similar to the United States’ VICTORY standard.
The standards above are beginning to define standard electrical interfaces on equipment, including connector specifications, sizes, platforms and pin assignment. Although these standards differ slightly in scope and content, they are driving toward the same basic principles: standardization and compatibility of vehicle systems and interfaces.
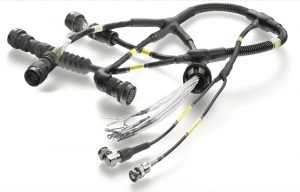
Impact of Standardization
Advancing Electrical Harness Design
A significant benefit of moving toward standardization is being able to use Commercial-Off-The-Shelf (COTS) components. Designed to specific standards (such as connectors types and pin assignments), COTS products enable manufacturers and support networks to keep replacement parts readily available for new designs or repairs. This situation stands in contrast to fully bespoke components. If a vehicle that uses custom components is damaged or requires maintenance, it could be out of action for months awaiting a custom replacement part. However, using COTS components can reduce repair and replacement times to hours or days.
Ground vehicle interconnect system designs have become increasingly complicated with limited continuity between designs. Allowing vehicle architects to source standardized systems from COTS components and suppliers allows more focus on the functionality and long-term repairability of systems, thereby reducing complexity of designs, improving performance and reducing costs. Currently, electrical designers face demanding challenges during the design process and can benefit from a one-stop source for military-standard interconnect systems. A fully integrated supply chain that offers all the required components and manufactures Military-Standard Interconnect Systems, along with design and engineering expertise, can be a valuable long-term partner.
Roadmap to the Future
Spec’d for Success
Working with a large supplier such as TE, designers can confidently make their product selection knowing a complete range of components are available that meet and exceed GVA, VICTORY, and other military standards. Given the challenges, complexity, and criticality of mission-ready harnesses and cabling, it’s advisable for designers to work with a knowledgeable supplier early in the design process. Engineering knowledge, offered by TE engineers who are experts in the needs of next-generation military applications, can guide users to the right set of components for their specific applications and standards.
TE has developed compatible systems of components for specific applications. Several examples of current end-to-end systems available are:
• TE System 25: Environmentally sealed, flame and fluid resistant system that is suited to rugged military vehicles, especially exposed or exterior applications.
• TE System 100: Sealed low-toxicity, low-smoke, zero-halogen system that is designed for confined, enclosed environments such as internal vehicle or marine areas.
• TE System 200: Sealed, high-temperature, and resistant to aggressive fluids. Suited to engine compartments or areas with prolonged, high-temperature exposure.
A leading global connectivity supplier for defense, TE is a one-stop-shop for harsh environment interconnect solutions. TE offers a fully integrated supply chain that includes wire and cable, tubing, molded parts, backshells and connectors from its Raychem, DEUTSCH, Polamco and AMP product families. Selecting from standardized systems and components, users can quickly design and implement requirements for future platforms.
Looking to the future, manufacturers could eventually produce power distribution units, power and data cables, connectors, various switches and other components that are pre-manufactured to the military standards of each country. This will allow for almost immediate demand satisfaction, a high-level of quality, and the ability to plug-and-play using standardized parts that put vehicles back at full force-readiness with minimal effort and cost.
The drive toward standardization will lead to a complete overhaul of the design process. The result would be improvements for everyone, starting with the system designer all the way through to the soldiers on the ground. Readily-available, standardized assemblies and systems are the future; military readiness and ground defense are depending on it.